Understanding Engine Bearing Cost: A Complete Guide for Business Owners
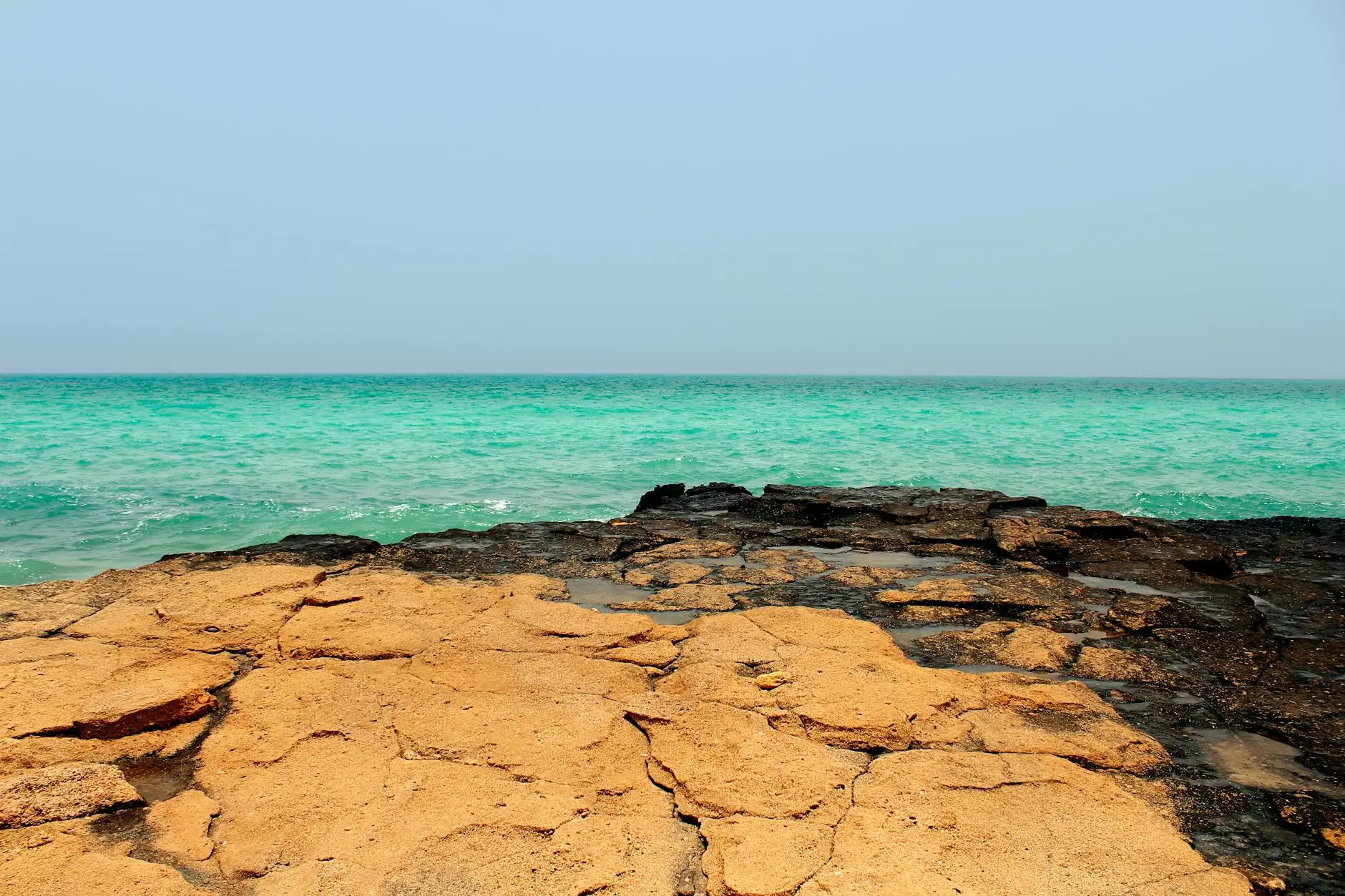
The importance of engine bearings cannot be overstated in the realm of diesel engines. As critical components that reduce friction and support engine components, knowing the engine bearing cost can significantly impact your overall maintenance budget and operational efficiency. This article will delve deeply into the factors affecting engine bearing costs, types of bearings, and how to make informed purchasing decisions to benefit your business.
What Are Engine Bearings?
Engine bearings are specialized components that provide a smooth surface for moving elements in an engine. These bearings help to:
- Reduce friction between moving parts
- Support rotating elements such as crankshafts and camshafts
- Absorb shock and reduce vibrations during engine operations
- Facilitate heat dissipation to prevent overheating
Understanding these functions is crucial when considering the engine bearing cost and the long-term implications of using quality parts in your diesel engines.
Factors Affecting Engine Bearing Cost
Various factors influence the cost of engine bearings, including:
1. Type of Engine Bearing
The type of bearing you choose will significantly affect the overall engine bearing cost. Common types include:
- Plain Bearings: Simplicity and durability make these a cost-effective option for many diesel engines.
- Rolling Element Bearings: While they offer lower friction, they tend to be more expensive due to their design complexity.
- Shell Bearings: Commonly used in large diesel engines, they can vary widely in price based on size and quality.
2. Material Quality
The material used in manufacturing engine bearings also impacts price. High-quality materials such as copper, lead, or aluminum alloys might cost more but provide superior performance and longevity, reducing the need for frequent replacements.
3. Brand Reputation
Renowned brands typically command higher prices due to their reputation for quality, reliability, and warranty offerings. It’s important to factor in what a specific brand brings to the table when assessing the engine bearing cost.
4. OEM vs Aftermarket Parts
Choosing between Original Equipment Manufacturer (OEM) and aftermarket parts can influence your costs. While OEM parts are often more expensive, they ensure perfect fit and finish, which can be critical in high-performance applications. Aftermarket options might be cheaper but come with the risk of variable quality.
The Importance of Sourcing Engine Bearings Wisely
Sourcing quality engine bearings from reputable suppliers is crucial in maintaining engine performance. Here are a few tips for sourcing:
- Research Suppliers: Utilize platforms like client-diesel.com to find trusted spare parts suppliers.
- Check Reviews: Prioritize suppliers with positive customer feedback regarding their product range and service quality.
- Understand Warranty Offers: Opt for suppliers that provide robust warranty terms, which can save you money over time.
Comparing Costs: OEM vs Aftermarket Engine Bearings
When evaluating engine bearing costs, a direct comparison between OEM and aftermarket options can provide clarity:
OEM Bearings
OEM bearings are manufactured to the exact specifications of the original parts. While they tend to cost more, they offer advantages such as:
- Guaranteed fit and compatibility
- Higher quality material and construction
- Better overall engine performance
- Manufacturer-backed warranties
Aftermarket Bearings
Aftermarket bearings can be significantly cheaper, making them attractive for budget-conscious operators. However, they may come with downsides, such as:
- Variability in quality
- Potentially higher failure rates
- Compatibility issues
- Limited or no warranties
Thus, the choice between OEM and aftermarket bearings should align with your business's operational strategies and budget constraints.
Estimating Your Total Engine Bearing Cost
When planning your budget for engine maintenance, it’s essential to consider various engine bearing costs, including:
- Initial Purchase Price: This is the basic cost of the bearings themselves.
- Installation Costs: Labor costs associated with installing the bearings should be calculated, as improper installation can lead to early failure and more expenses.
- Replacement Intervals: Some bearings may need to be replaced more frequently than others, so consider the frequency of replacement in your total cost calculation.
- Downtime Costs: Consider the potential loss in productivity or sales if the engine fails, leading to your operational time being affected.
Tips for Reducing Engine Bearing Costs
Reducing engine bearing costs doesn't necessarily mean compromising on quality. Here are some strategies:
- Regular Maintenance: Implementing a robust maintenance schedule can significantly extend the life of your bearings, reducing replacement frequency.
- Correct Usage: Use engines according to the manufacturer's specifications and recommendations to avoid undue strain on bearings.
- Invest in Quality: Always opt for quality parts – they may cost more upfront but will save you money in the long run.
- Negotiation: Don’t hesitate to negotiate prices with suppliers – bulk purchases can leverage pricing advantages.
Conclusion: Making Informed Decisions on Engine Bearings
In summary, understanding the engine bearing cost is vital for any business that depends on diesel engines. By factoring in various elements such as type, quality, brand reputation, and sourcing wisely, you can make informed decisions that will save you money and enhance your operations. Remember to consider maintenance and replacement intervals as part of your total cost analysis.
For top-quality diesel engine parts and expert service, visit client-diesel.com today and ensure your business stays on the road to success with reliable and cost-effective engine bearing solutions.