Understanding Car Parts Mold: A Comprehensive Guide
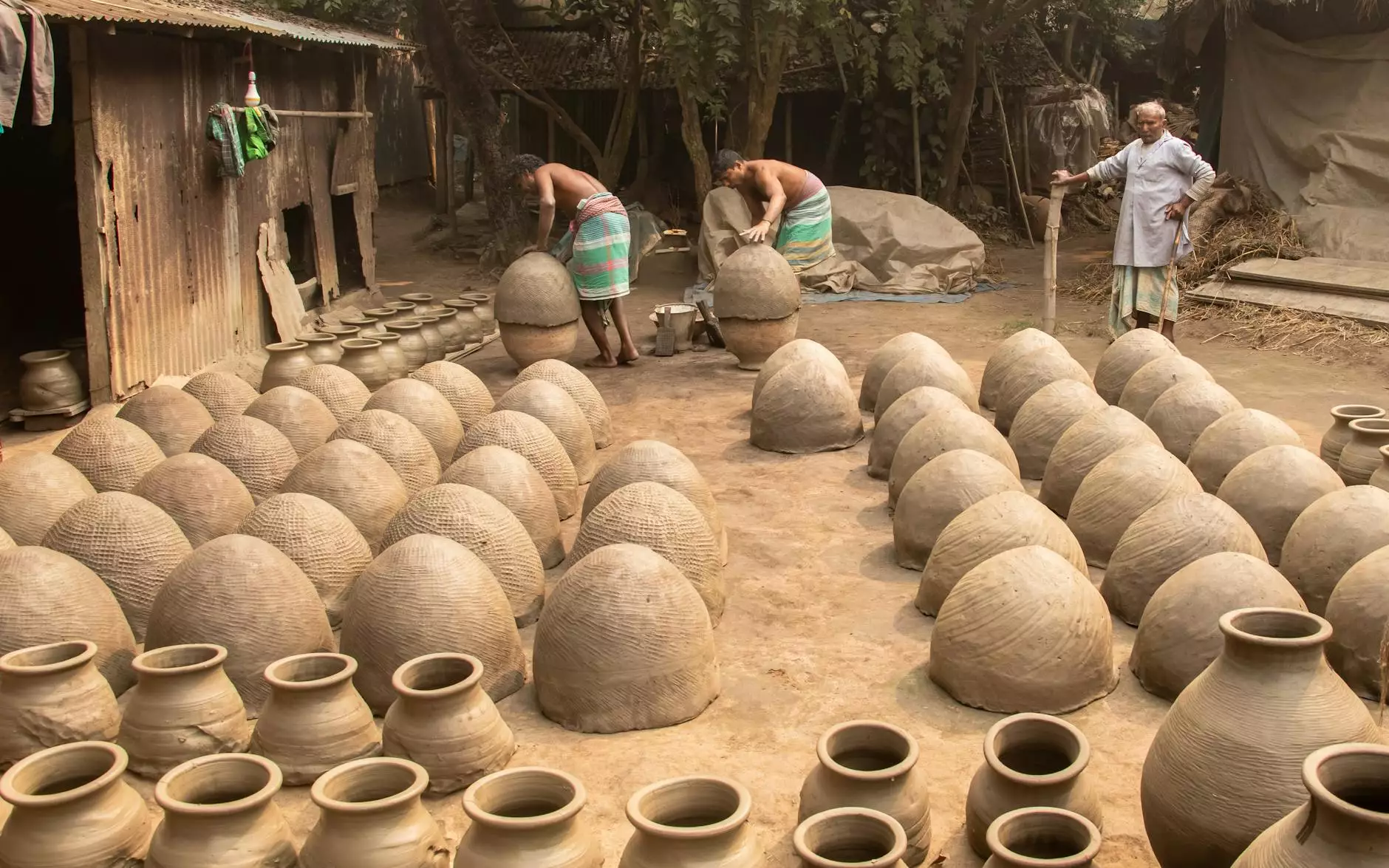
The automotive industry is a key player in the global economy, constantly innovating and evolving to meet consumer needs. Among the many critical components that ensure the functionality and safety of vehicles, the car parts mold stands out as a fundamental element in manufacturing high-quality automotive parts. In this article, we will dive deep into the concept of car parts molds, their importance in the manufacturing process, and the role of metal fabricators in producing these essential molds.
What is a Car Parts Mold?
A car parts mold is a hollow container used to create a specific shape by shaping liquid or pliable materials, such as metal, plastic, or rubber. These molds are integral in the production of automotive components, ensuring that each part is consistent in quality and fit. They are crafted with precision to meet the exact specifications needed for each component, whether it be for the engine, body, or interior parts of a vehicle.
The Importance of Car Parts Molding in the Automotive Industry
The process of molding car parts is not only about crafting shapes; it plays a crucial role in the durability, quality, and performance of automotive products. Here are some reasons why car parts molds are essential:
- Precision Manufacturing: Molds allow for high-precision manufacturing, which is critical for vehicle safety and performance.
- Cost Efficiency: By utilizing molds, manufacturers can produce parts in bulk, reducing costs per unit while maintaining quality.
- Material Versatility: Molding accommodates a wide range of materials, allowing manufacturers to choose the best options for different components.
- Design Flexibility: Molds can be designed to create complex shapes that would be challenging to achieve through other manufacturing methods.
Types of Car Parts Molds
Car parts molds can be categorized based on the materials they are designed to work with and the types of processes they utilize. Here are some of the most common types:
1. Injection Molds
Injection molding is a widely used process in the automotive sector, especially for plastic parts. The process involves injecting molten plastic into a mold where it cools and solidifies into the required shape. This method is ideal for producing intricate designs with high tolerances.
2. Blow Molds
Blow molding is used to create hollow plastic parts. It is particularly effective for producing containers and various components like fuel tanks and ducts. The process involves inflating a soft plastic tube within a mold to form the desired shape.
3. Compression Molds
Compression molding usually involves putting raw material in a heated mold. The material is compressed into the shape of the mold and then cured. It is commonly used for rubber and composite materials used in certain automotive parts.
4. Die Casting Molds
Die casting involves forcing molten metal into a mold to create metal parts. This method is efficient for producing complex shapes with excellent surface finish and dimensional accuracy, making it suitable for engine components and gearbox housings.
The Role of Metal Fabricators in Mold Manufacturing
Metal fabricators play a pivotal role in the creation of car parts molds. They are responsible for designing and manufacturing molds that meet specific performance standards and tolerances. Here’s how metal fabricators contribute to mold production:
1. Design and Engineering
Metal fabricators work alongside engineers to design molds that are not only functional but also efficient. Through advanced CAD software, they ensure that designs are tailored for optimal production efficiency.
2. Material Selection
The choice of materials used to create molds is critical. Metal fabricators select suitable alloys and steels that can withstand high temperatures and pressures, ensuring longevity and performance under operational conditions.
3. Precision Machining
Using state-of-the-art machining equipment, metal fabricators meticulously manufacture molds to achieve the necessary tolerances and surface finishes required for high-quality production.
4. Maintenance and Repair
Ongoing maintenance is essential for mold longevity. Metal fabricators provide repair services to keep molds in optimal working condition, which is crucial for preventing defects in mass-produced parts.
Challenges in Car Parts Mold Manufacturing
While the manufacturing of car parts molds is a critical process, it is not without its challenges. Here are some key issues faced by manufacturers:
1. High Production Costs
The initial costs associated with designing and manufacturing molds can be substantial. However, these costs are often offset by the efficiencies gained during mass production.
2. Complexity of Designs
As automotive designs become more complex, so do the molds required to produce them. This complexity can lead to longer lead times and increased costs.
3. Material Limitations
Not all materials are suitable for every type of molding process. Choosing the wrong material can lead to production issues and compromised part performance.
Future Trends in Car Parts Mold Manufacturing
As the automotive industry continues to evolve, so do the techniques and technologies used in car parts mold manufacturing. Here are some trends that are shaping the future:
1. Advancements in 3D Printing
3D printing technology is allowing for faster prototyping and testing of molds. This rapid iteration process can reduce time-to-market for new automotive parts.
2. Sustainable Practices
With increasing focus on sustainability, manufacturers are seeking eco-friendly materials and processes. This includes using recyclable materials for molds and reducing waste during production.
3. Smart Manufacturing
The integration of IoT (Internet of Things) in manufacturing processes is leading to smarter and more efficient operations. Real-time data on mold performance can help manufacturers optimize their processes.
4. Customization and Flexibility
As consumer preferences shift, there is a growing need for customizable automotive parts. Molding technology is likely to adapt to produce smaller batches of diverse components efficiently.
Conclusion
In conclusion, the significance of car parts molds in the automotive industry cannot be overstated. They are a cornerstone of manufacturing high-quality, reliable, and safe automotive components. As we have explored, metal fabricators play an essential role in the design, production, and maintenance of these molds, ensuring that the automotive industry can continue to thrive amid rapid technological advances and changing consumer demands.
By understanding the intricacies of car parts molds, manufacturers can better navigate the challenges of production and take advantage of emerging trends to stay competitive in the global market.
For more information about high-quality car parts mold manufacturing, visit deepmould.net.